How to build a well house? This comprehensive guide provides a detailed roadmap for constructing a functional and aesthetically pleasing well house, from initial planning to final maintenance. We’ll explore the various types of well houses, essential design considerations, construction materials, and installation procedures, ensuring a safe and successful project.
Discover the key factors to consider when planning your well house, including local regulations, water source requirements, and the unique characteristics of different well house designs. This guide is your essential resource for building a well house that meets your specific needs and adheres to industry best practices.
Introduction to Well Houses
A well house is a structure specifically designed to house and protect a well, providing access for maintenance and preventing contamination. It’s a vital component of a water supply system, ensuring the safety and reliability of the water source. Its presence is critical in areas with limited surface water access or where groundwater is the primary water source.The primary purpose of a well house is to safeguard the well from environmental factors that could compromise water quality.
This includes protecting the well from surface contaminants, extreme temperatures, and physical damage. It also facilitates the efficient extraction and distribution of water.
Types of Well Houses
Well houses come in various forms, each with its own set of advantages and disadvantages. Understanding these differences is crucial for selecting the appropriate design for a specific site and budget. The two primary types are above-ground and below-ground well houses.
Comparison of Well House Types
Feature | Above-Ground | Below-Ground |
---|---|---|
Construction | Typically built using concrete, wood, or metal framing. Above-ground well houses are often simpler and quicker to construct. | Often constructed using reinforced concrete, providing a more robust and durable structure. The depth of the well house may require specialized excavation equipment. |
Cost | Generally less expensive to build than below-ground well houses due to the simpler construction methods and reduced excavation costs. | More expensive due to the added excavation, concrete reinforcement, and potential need for specialized equipment. |
Aesthetics | May be more visible and impactful on the surrounding landscape. Aesthetics can be customized to fit various architectural styles. | Often blends more seamlessly into the landscape, offering a more discreet aesthetic. Landscaping can help to further integrate it. |
Maintenance | Easier to access and maintain, as the well is readily visible. Regular inspections and repairs are more straightforward. | May require more specialized equipment or procedures for access and maintenance. Regular inspections are still essential to ensure the well’s integrity. |
Historical Context of Well Houses, How to build a well house
Well houses have a long history, dating back to ancient civilizations. Early well houses were often simple structures built to protect wells from contamination and provide access for water collection. As communities grew and water became more critical, well houses evolved in design and complexity to meet the changing needs of society. The design and materials used varied significantly based on the availability of resources in different regions and eras.
This evolution demonstrates the importance of well houses throughout history in ensuring a safe and reliable water supply.
Planning and Design
A well house, crucial for a safe and reliable water supply, demands meticulous planning and design. Proper planning ensures the well house effectively protects the water source, complies with local regulations, and optimizes functionality. A well-designed well house will safeguard the water quality and longevity of the entire system.Careful consideration of various factors, including water source characteristics and local building codes, is essential for the well house’s success.
A well-conceived design translates into a structure that’s both functional and aesthetically pleasing.
Importance of Proper Planning
Proper planning for a well house is paramount. A well-thought-out plan prevents costly mistakes and ensures the well house meets its intended purpose. This includes anticipating potential issues and incorporating solutions in the design phase, rather than addressing them later.
Factors to Consider When Designing a Well House
Several key factors influence the design of a well house. These include the type of water source, the local building codes and regulations, and the specific needs of the property.
- Water Source Characteristics: The well’s depth, aquifer type, and water quality influence the well house’s design. A shallow well requires a different design than a deep well, considering factors like potential for flooding or soil conditions.
- Local Regulations: Building codes and zoning ordinances vary significantly. Adherence to these regulations is crucial to avoid permit issues and ensure compliance. Consult with local authorities to understand the specific requirements.
- Property Needs: The well house should accommodate the water needs of the property. Factors such as the number of occupants, water usage patterns, and potential future expansion should be considered. Consider if the well will serve only the house, or if it’s intended for multiple buildings or irrigation.
- Environmental Factors: The local climate, soil type, and potential for flooding should be considered. A well house design needs to be durable and resilient enough to withstand the local conditions. This includes considerations for seismic activity in areas prone to earthquakes.
Essential Components of a Well House Design
A well house’s design must include essential components for safety, functionality, and compliance. These elements contribute to a well-functioning and protected water source.
- Well casing: The casing protects the well from surface contamination and collapse. Its material and depth are crucial design aspects. Consider factors such as corrosion resistance and appropriate diameter.
- Water pump: The pump’s type and capacity should be chosen based on the water demand. The design should account for pump placement and access for maintenance.
- Water treatment system: If necessary, a water treatment system is incorporated to address water quality issues like iron, sediment, or other contaminants. The type of treatment and its location within the well house are crucial elements.
- Electrical wiring and plumbing: These systems need to be carefully planned for functionality and safety. Consider the location of electrical panels, and the correct placement of water pipes for optimal flow and pressure.
- Access and ventilation: Adequate access for maintenance and ventilation to prevent moisture build-up are vital. Design should account for proper air circulation.
Example of Well House Layouts
Well house layouts can be adapted to various needs and site conditions.
Layout Type | Description | Suitability |
---|---|---|
Traditional Well House | A simple, rectangular structure. Often used for smaller properties with a single well. | Ideal for basic well systems in areas with moderate water needs. |
Elevated Well House | The well house is elevated above ground level. Provides better protection against flooding. | Suitable for areas with high water tables or potential flooding. |
Modular Well House | Pre-fabricated components are assembled on-site. Offers faster installation. | Efficient for situations requiring rapid installation or when site access is limited. |
Properly designed and constructed well houses are crucial for the reliable and safe operation of well systems, ensuring a long and efficient service life.
Diagram of a Well House Design
(A detailed diagram would be provided here, describing the components of a well house, including the well casing, pump, electrical and plumbing connections, and ventilation. The diagram should illustrate a typical well house design, showcasing the location of various elements.)
Construction Materials and Methods
Constructing a well house requires careful consideration of materials and methods to ensure durability, longevity, and cost-effectiveness. Proper selection depends on the intended use, local climate conditions, and the budget. The right approach ensures a safe and functional structure that protects the well and maintains its integrity.Well house construction involves a range of materials and methods, each with its own set of advantages and disadvantages.
Choosing the appropriate combination optimizes the structure’s functionality and lifespan. The construction process should be carefully planned and executed to ensure the well house’s structural integrity and longevity.
Common Construction Materials
Various materials are suitable for well house construction, each offering unique properties. Concrete, wood, and steel are common choices, each with its own advantages and limitations.
- Concrete: Concrete is a popular choice due to its strength and durability. It can withstand significant stress and is relatively resistant to moisture and pests. Precast concrete sections or poured-in-place concrete are frequently used for well house foundations and walls.
- Wood: Wood is often used for framing and cladding, offering a more aesthetically pleasing appearance. However, wood is susceptible to rot, decay, and insect infestation if not treated properly. Pressure-treated lumber can extend its lifespan but may still require periodic maintenance.
- Steel: Steel provides exceptional strength and resistance to corrosion when properly protected. Steel framing or cladding is suitable for well houses needing significant structural support, especially in areas with high seismic activity. However, the initial cost of steel may be higher compared to other materials.
Construction Methods
Different methods exist for constructing well houses, each influencing the overall cost, time, and quality of the structure.
- Poured Concrete: Poured concrete involves pouring concrete into a prepared formwork. This method provides a strong and durable structure but can be labor-intensive and time-consuming. Precise formwork is crucial to achieve the desired shape and dimensions.
- Prefabricated Well Houses: Prefabricated well houses are pre-assembled units that can be transported and assembled on-site. This method is generally faster and more efficient, but the design options may be limited compared to custom-built structures. Quality control during the manufacturing process is paramount.
Material and Method Comparison
The choice of material and method significantly impacts the cost and durability of the well house.
Material | Cost | Durability | Maintenance |
---|---|---|---|
Concrete | Moderate | High | Low to Moderate (depending on finishing) |
Wood | Low to Moderate | Moderate (with proper treatment) | Moderate to High (periodic treatments needed) |
Steel | High | Very High | Low (with proper coatings) |
Note: Costs are relative and can vary based on location, labor rates, and specific material choices. Durability ratings are relative to the material’s expected lifespan and potential deterioration under normal use.
Installation and Setup
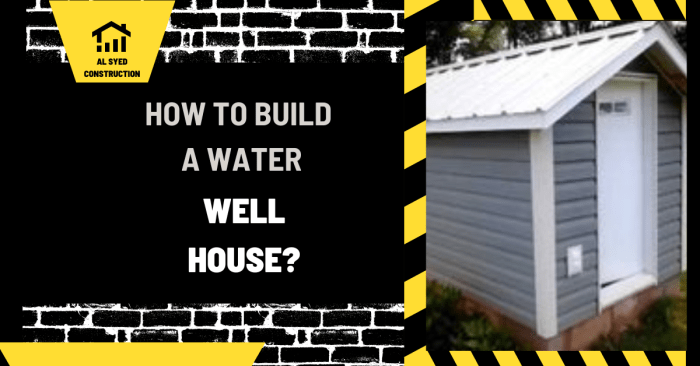
Installing a well house involves meticulous planning and execution to ensure proper functionality and safety. Careful attention to detail during this phase will contribute to the long-term reliability and efficiency of the entire system. Proper installation safeguards the well from contamination and the plumbing system from leaks and damage.
Installation Steps
This section details the crucial steps for installing a well house, from initial preparation to final connections. Adherence to these steps ensures a secure and functional well house.
- Foundation Preparation: Ensure the foundation is level and stable to support the well house structure. Use appropriate leveling tools and techniques to achieve a solid base. This crucial step prevents future structural issues and ensures the well house sits correctly relative to the ground. Any unevenness or instability can lead to problems with the well’s function and structural integrity.
- House Plumbing Connection: Connect the well to the house’s plumbing system. This includes installing the appropriate piping, valves, and fittings to allow water flow from the well to the house. Use proper pipe sealant to prevent leaks. Precise and careful connections minimize the risk of leaks, which can cause damage to the property and the surrounding environment.
- Well House Assembly: Carefully assemble the well house components according to the manufacturer’s instructions. Verify all connections and ensure the structure is securely anchored to the foundation. A stable and securely assembled well house is essential for the long-term functionality and safety of the entire system. This step requires adherence to manufacturer guidelines for structural integrity.
- Sealing and Insulation: Seal all joints and openings in the well house to prevent water leakage and maintain proper insulation. Use appropriate sealants and insulation materials for the climate and environment. Proper sealing and insulation are vital to prevent water damage, temperature fluctuations, and contamination of the well water.
Connecting the Well to the House Plumbing System
Correctly connecting the well to the house plumbing system is essential for efficient water supply. This step involves several critical procedures.
- Pipe Selection: Choose PVC or copper pipes suitable for potable water and compatible with the well’s pressure and flow rate. Using incorrect pipe types can lead to leaks, reduced flow, and potential health hazards.
- Fitting Installation: Use appropriate fittings to connect the well pipe to the house plumbing system. Properly installed fittings ensure a secure connection, minimizing the risk of leaks and ensuring smooth water flow.
- Pressure Relief Valve: Install a pressure relief valve to prevent excessive pressure buildup in the system. This safety measure is essential to avoid potential pipe damage or water damage to the property.
Importance of Sealing and Insulation
Proper sealing and insulation are vital for maintaining the quality of well water and protecting the well house structure. This includes several critical steps.
- Preventing Water Leakage: Seal all joints and openings to prevent water leakage, which can lead to contamination of the well water and structural damage to the well house.
- Maintaining Temperature Regulation: Insulation helps maintain optimal water temperature, preventing excessive heating or cooling, which can impact water quality.
- Protecting from Contamination: A well-sealed and insulated well house helps protect the well water from contamination by external elements. This ensures the safety and quality of the water supply.
Safety Precautions
Safety is paramount during well house installation. Adherence to safety protocols protects workers and ensures the well house is installed correctly.
- Protective Gear: Always wear appropriate safety gear, such as gloves, safety glasses, and steel-toed boots, to prevent injuries.
- Electrical Safety: Exercise caution around electrical components during the installation process. Disconnect power sources as needed to prevent electrical hazards.
- Proper Lifting Techniques: Use proper lifting techniques when handling heavy materials to avoid back injuries.
Tools Required for Installation
A comprehensive list of tools is essential for the successful installation of a well house.
Tool Category | Specific Tools |
---|---|
Plumbing | Pipe cutters, pipe wrenches, pipe sealant, PVC cement, couplings, valves, etc. |
Electrical | Wire strippers, wire connectors, electrical tape, voltage testers, etc. |
Construction | Level, measuring tape, drill, screwdriver, safety glasses, work gloves, etc. |
Maintenance and Troubleshooting
Proper maintenance is crucial for the longevity and reliable operation of your well house system. Regular checks and preventative measures can significantly reduce the risk of costly repairs and ensure a consistent water supply. Addressing issues promptly is key to avoiding larger problems down the road.Routine maintenance, combined with proactive troubleshooting, is essential for maintaining a well-functioning well house system.
This includes identifying and addressing potential problems before they escalate into major issues, saving you time, money, and frustration.
Routine Maintenance Schedule
Regular inspection and maintenance are critical to preventing potential problems. A well-maintained well house system will operate efficiently and reliably for years. A consistent schedule helps ensure that critical components are inspected and serviced on a timely basis.
- Inspect the well casing and surrounding area for signs of cracks, settling, or erosion at least every three months.
- Check the pump motor and pump components for any signs of damage, such as overheating, unusual noises, or loose connections, every month. This includes the pump’s electrical connections and any other components connected to the pump system.
- Examine the well house’s exterior for signs of water damage, leaks, or corrosion every two months.
- Clean the well house exterior and surrounding area to prevent the buildup of debris and ensure proper ventilation. Regular cleaning prevents clogging and ensures proper airflow.
- Test the well water quality and flow rate quarterly. This helps ensure that the water quality remains consistent and that the flow rate is adequate for your needs. Changes in water quality or flow can indicate potential problems.
Leak Detection and Repair
Identifying and repairing leaks promptly is vital to preventing water damage and structural issues within the well house. Early detection often translates to lower repair costs and prevents more extensive damage.
Constructing a well house involves careful planning and execution. Consider the local regulations, and remember to consult with professionals like plumbers. For financial support, you might want to check out the local bank, Cadence Bank in Amory, MS , which is known for its excellent services to homeowners. Properly securing your well house ensures a reliable water source for your home.
- Regularly check for signs of water pooling around the well house, or dampness on the interior walls.
- Inspect all connections, including pipes, fittings, and seals, for any signs of leakage. Look for drips, stains, or moisture buildup.
- Use a moisture meter to identify hidden water damage, especially if you suspect leaks within the well house’s walls or foundation.
- If a leak is detected, promptly address the issue to prevent further damage. Consult a professional if necessary.
Pump Troubleshooting Guide
A well pump failure can disrupt your water supply. A step-by-step approach to troubleshooting pump malfunctions can save time and money.
- Check the power supply. Verify that the electrical connection to the pump is secure and that the breaker is turned on. If the power supply is faulty, this is the first place to look.
- Listen for unusual noises. Unusual noises, such as grinding or humming, can indicate a mechanical problem with the pump.
- Check the water level in the well. If the water level is too low, the pump may not be able to draw water. Ensuring the water level is appropriate for the pump is crucial.
- Inspect the pump’s pressure switch. A faulty pressure switch can prevent the pump from operating correctly.
- Consult a qualified well technician if the problem persists. A professional can diagnose the issue accurately and perform the necessary repairs. Avoid attempting repairs if you lack the necessary expertise.
Preventive Maintenance Tips
Implementing preventative measures can significantly reduce the likelihood of future problems. Proactive measures help extend the life of the well house and ensure a continuous supply of clean water.
- Use a quality well pump that’s designed for your specific well conditions. Ensure the pump is compatible with the well’s capacity and water pressure.
- Protect the well house from extreme weather conditions. Extreme weather can lead to damage, and appropriate protection is necessary.
- Regularly inspect and maintain the well casing to prevent damage. Proper well casing protection prevents leaks and extends the life of the well.
- Follow the manufacturer’s recommendations for the pump and other components. Understanding and adhering to manufacturer guidelines can greatly improve the well’s performance and life expectancy.
Legal and Regulatory Considerations: How To Build A Well House
Building a well house requires careful consideration of local regulations and permits. Ignorance of these requirements can lead to costly delays, construction issues, or even legal penalties. This section details the critical legal aspects to ensure a compliant and safe well house installation.Understanding and adhering to local regulations is paramount for a smooth and successful well house project.
These regulations often vary by jurisdiction and are designed to protect public health, safety, and the environment. Failure to comply can result in significant problems, including project halting, costly corrections, and potential legal action.
Local Regulations and Permits
Local building codes and ordinances govern well house construction. These regulations often specify the required depth and diameter of the well, the materials that can be used, and the methods for construction and installation. Compliance with these regulations is crucial for ensuring the safety and functionality of the well house. A crucial part of the process is obtaining the necessary permits from the relevant local authorities.
Building Codes
Building codes provide standards for construction, ensuring the structural integrity and safety of the well house. These codes dictate the minimum requirements for materials, design, and construction techniques. Adherence to building codes is essential to avoid structural problems and ensure the safety of the well house and surrounding areas. Furthermore, building codes usually include requirements for plumbing and electrical connections, ensuring the safety and functionality of the well house systems.
Common Regulations and Implications
- Well Depth and Spacing Requirements: Local regulations often dictate the minimum depth and maximum spacing between wells. Exceeding these limits can lead to contamination issues, impacting the water quality for both the homeowner and the broader community. For instance, exceeding the maximum spacing between wells might cause water flow issues and contamination, impacting the entire neighborhood.
- Water Quality Standards: Regulations regarding water quality and testing are essential. These standards help to maintain the purity and safety of the water source. Examples include requirements for well casing materials, well sealing, and regular water quality testing to ensure the safety and potability of the water supply.
- Septic System Regulations: If a septic system is present on the property, regulations regarding its location and proximity to the well house must be followed. Improper placement can contaminate the well water, causing serious health risks. For instance, if a septic tank is located too close to the well, it could leach contaminants into the well water, leading to a potential health hazard.
- Environmental Regulations: These regulations often address issues like groundwater protection, conservation, and waste disposal. They can impact the design and construction of the well house to protect the environment. For example, regulations might dictate the type of insulation used, prohibiting harmful substances that can leach into the ground water.
Homeowner Responsibilities
Homeowners bear the responsibility for ensuring proper well maintenance and safety. This includes regular inspections, adherence to maintenance schedules, and reporting any issues to the appropriate authorities. Regular maintenance and inspections are critical to prevent potential problems. Furthermore, understanding and adhering to safety procedures around the well house is essential to avoid accidents. Regular testing and monitoring of the well water are also crucial for identifying potential contamination issues.
Building a well house involves careful planning and precise measurements. For instance, consider the structural integrity of the walls and the size of the well itself. To ensure your party’s success, exploring delicious Minecraft-themed food ideas, like a “Creeper” cake or a “Pig” pizza, from minecraft food ideas for party , will definitely elevate the overall experience.
Ultimately, a sturdy well house will require solid foundations and appropriate materials, ensuring a safe and reliable water source.
Examples and Case Studies
Understanding the practical application of well house design is crucial. Real-world examples demonstrate the successful implementation of various approaches, showcasing successful projects, challenges overcome, and valuable lessons learned. These case studies provide insights into diverse well house designs and the factors that contribute to their effectiveness.Well house projects vary significantly depending on the specific needs and environmental conditions.
From simple, functional designs to elaborate, aesthetically pleasing structures, each project presents unique considerations regarding materials, construction methods, and maintenance strategies. By analyzing these case studies, we can gain a deeper understanding of the process and identify key elements for building a well house that meets specific requirements.
Rural Residential Well House Project
This project involved constructing a well house for a rural home in a region with challenging soil conditions. The primary goal was to create a durable and aesthetically pleasing structure that would withstand harsh weather.
- The design incorporated a reinforced concrete foundation to address the soil issues. A sturdy steel frame provided support for the roof, protecting the well pump and equipment from the elements.
- The exterior walls were constructed from insulated, weather-resistant composite panels, providing thermal efficiency and protection against moisture. This design element contributed significantly to the longevity of the structure.
- The interior of the well house was designed with accessibility in mind, including ample space for maintenance and repair work. This consideration proved vital in preventing future complications during upkeep and maintenance.
- The project successfully demonstrated how careful design and material selection could create a robust well house in a demanding environment.
Urban Apartment Complex Well House
This project involved the construction of a well house servicing a multi-unit apartment building in a densely populated urban area. The primary concern was maximizing space and minimizing disruption during construction.
- A compact, modern design was chosen, maximizing vertical space and utilizing minimal footprint. This was critical for the limited space available in the urban setting.
- The construction process was carefully planned to minimize disruption to the surrounding tenants. This involved strategic scheduling and coordination with the apartment building management.
- The well house was constructed using prefabricated components, enabling faster installation and reducing on-site labor. This approach significantly streamlined the construction timeline and contributed to project efficiency.
- The project showcased the potential for building functional well houses in urban environments by employing innovative construction techniques and designs.
Coastal Well House with Salinity Considerations
This project involved building a well house in a coastal area with high salinity levels. The primary challenge was to prevent corrosion and maintain the functionality of the well pump and equipment.
- The well house was designed with corrosion-resistant materials, such as stainless steel for the pump enclosure and specialized coatings for the interior surfaces. This crucial design feature was vital for the project’s success in a high-salinity environment.
- The project employed a specialized well casing material to prevent salt water intrusion into the well, ensuring the quality of the water supply. This design consideration ensured the long-term sustainability of the water source.
- A robust filtration system was integrated into the well house to address the salinity concerns. The filter system removed dissolved salts from the water, ensuring its suitability for consumption.
- This case study effectively demonstrated the importance of adapting well house design to specific environmental conditions and considering potential challenges, such as salinity, to ensure successful implementation.
Concluding Remarks
In conclusion, building a well house is a rewarding project that requires careful planning, meticulous execution, and a commitment to safety. By following this comprehensive guide, you can construct a well house that not only meets your water needs but also enhances the aesthetic appeal of your property. Remember to prioritize safety and compliance with local regulations throughout the entire process.
We hope this guide has been informative and helpful for you.
Top FAQs
What are the typical costs associated with building a well house?
The cost of building a well house varies greatly depending on factors like the size, materials used, complexity of the design, and local labor costs. Detailed cost estimates can be found by consulting with contractors and referencing material pricing guides.
What are some common problems with well houses, and how can they be addressed?
Common issues include leaks, pump malfunctions, and issues with the plumbing system connecting the well to the house. Addressing these issues often requires professional assistance from a qualified plumber or well technician. Regular maintenance and prompt attention to potential problems are crucial to avoid more extensive and costly repairs.
What permits and inspections are necessary for well house construction?
Local building codes and regulations will dictate the specific permits and inspections required. Always check with your local authorities for the specific requirements in your area. Failing to obtain necessary permits could lead to significant delays or even project rejection.
What are the different types of well houses, and which is best suited for my needs?
Well houses can be above-ground or below-ground, each with its own advantages and disadvantages. Above-ground well houses offer easier access for maintenance but may require more land space. Below-ground well houses are more aesthetically integrated but often involve more complex excavation and construction. Your choice should depend on factors like your budget, local regulations, and desired aesthetic.